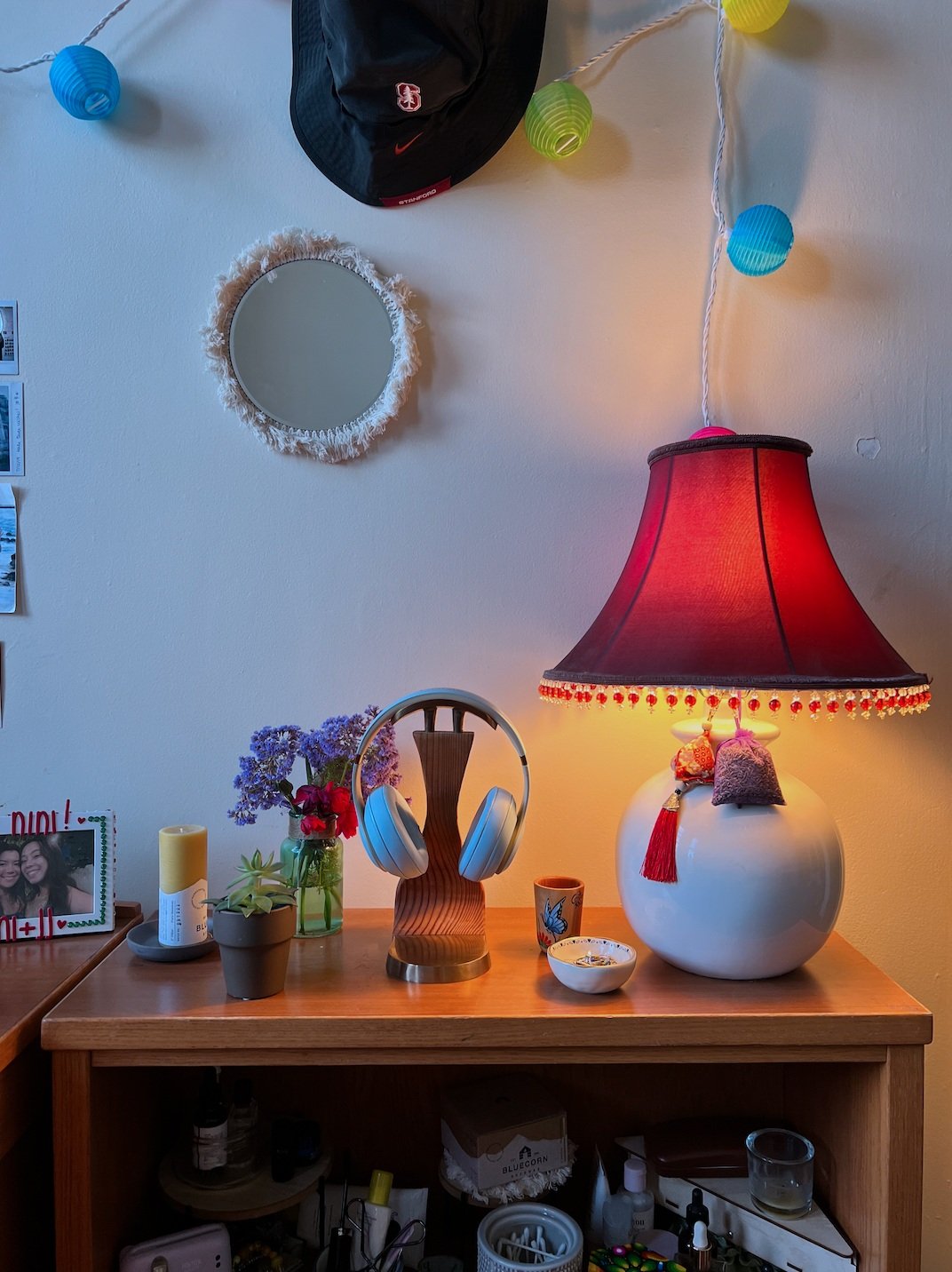
A home for your headphones.
Project Brief
The Rundown
The Details
Create a product using two manufacturing processes in a 5 week design sprint.
Inspired by my love of music and nature, the Headset Habitat combines functionality and aesthetics into a usable piece of room decor. Acting as 3 movable parts - the bronze headrest, the wooden neck, and bronze base - Headset Habitat is compact and can be easily packed and transferred for all of the journeys that you embark on.
Lathe and Mill processes
3D CAD - Autodesk Fusion 360
Bronze Casting
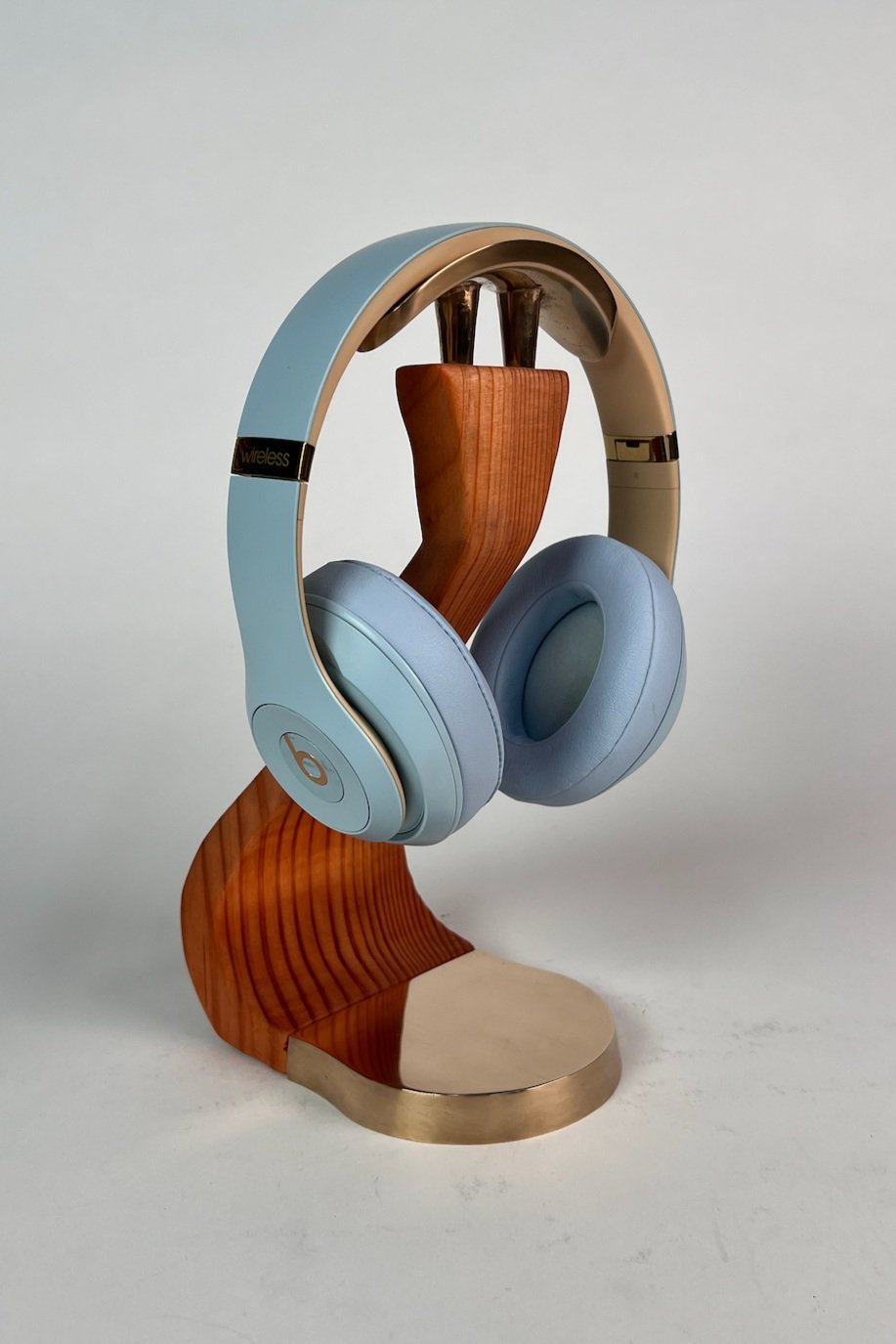
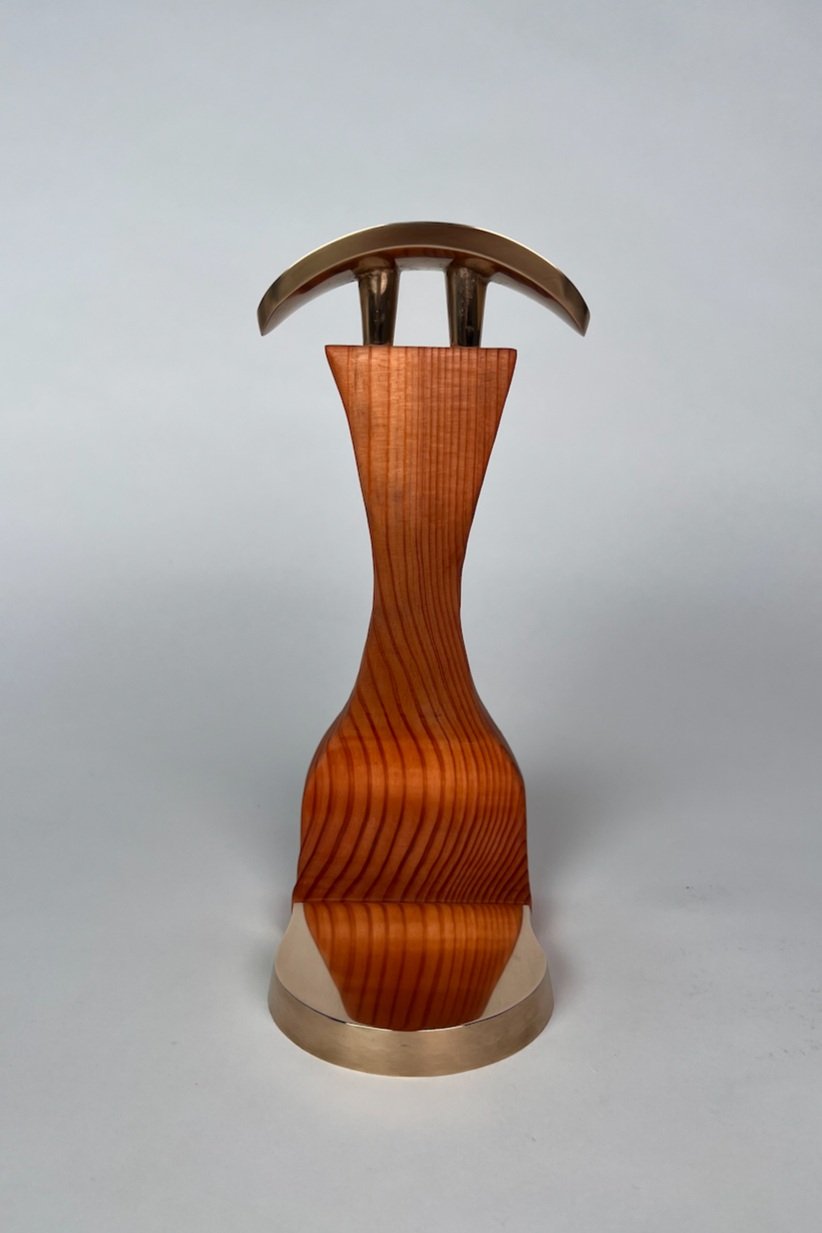
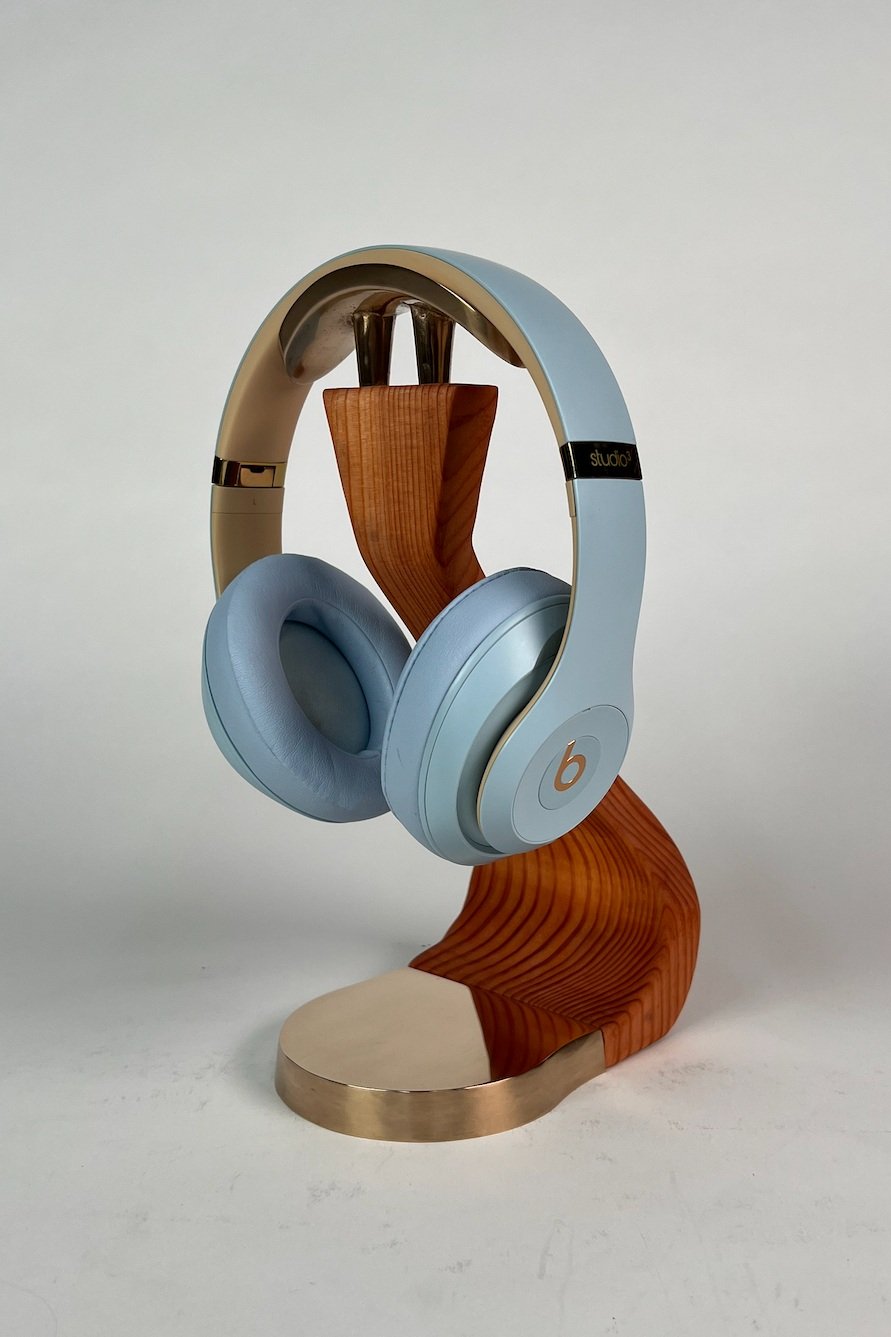
Design for Manufacturability
CAD
I began by CADing my headrest and base, as these 3D prints would be used as molds for the sand casting. In order to create successful sand mold, I CADed a base for my headrest due to its unusual shape. For both the headrest and the base, I made sure to add a 25% draft to all sides so that it allowed for an easy pull from the sand. The rectangular piece attached to the pieces is called a gate and runner which guides the molten metal into the sand cavity.
3D printing
Once my CAD was finalized, I 3D printed and sanded both parts to smooth down any rough edges. I then applied Shellac to fill in gaps and achieve a smooth finish so the casted part would be as smooth as possible.
Sand Casting
I first created the sand mold of my base as the shape was simple and I knew I would have more success with it. Creating the sand cast for my headrest was much harder but after 12 attempts, I finally had a successful mold! Everyone in the foundry celebrated with me :)
Metal Work
After both pieces had been poured successfully, I began to sand and clean up the sandy surfaces. I used the vertical mill to carve out a slot that would lock perfectly with the wooden part of my headphone holder.
Woodwork
To create the wooden neck of my headphone holder, I drew the outline of the body on a block of wood and slowly carved the excess wood away using a vertical bandsaw. I then used a belt sander and spindle sander to achieve smooth surfaces.
Finishing touches
Using 100 - 1000 grit sand paper, it took me 7 hours to sand my bronze base and headrest to a mirror finish. I also stained my wooden neck a cherry red and slid all of the pieces together.
Thanks for visiting!
Final Thoughts
In building the Headset Habitat, I learned how to scope projects with limited materials and a short timeline, all while learning new skills. Spending 15 hours a week in the machine shop allowed me to experience the value in learning from my peers, offering support to those around me, and celebrating others’ success.
I can now confidently CAD unusual shapes, do sand castings, operate the vertical mill, bandsaw and spindle sander. I also learned a valuable lesson on how to keep an open mind and view ‘challenges’ as an invitation to explore different design routes. The photos here don’t encapsulate all of the mistakes I made along the way, but I am now confident and excited to embrace future challenges head on in my design journey.